
86 17344894490
service@chalcoaluminum.com
- Opferanode aus Aluminiumlegierung
- Opferanode aus Magnesiumlegierung
- Beeindruckte aktuelle kathodische Schutzserie
Extrudierte Aluminiumprofil-Strukturteile im Fahrzeugbau
Den Informationen zufolge handelt es sich bei rund 60% der bestehenden Bestellungen europäischer Lokomotiv- und Fahrzeughersteller um Fahrzeuge mit Aluminiumkarosserie. Vor 20 Jahren betrugen solche Bestellungen nur 2% - 3%. Jetzt wurde die Aluminiumstruktur in Eis, tgv-2n, etr460, etr500, Talgo Hotel Zug und anderen Hochgeschwindigkeitszügen sowie vielen S-Bahn- und Stadtbahnfahrzeugen angewendet.
Die Einführung von extrudierten Aluminiumprofil-Strukturteilen begann in den frühen 1970er Jahren. Zu dieser Zeit hatte der wissenschaftliche und technologische Fortschritt in der Anwendung von Aluminiumprofilen es ermöglicht, Aluminiumkomponenten entsprechend der erforderlichen Form und Größe herzustellen. Diese Aluminiumkomponente wurde auf die kippbare Karosserie von apt-Zügen in Großbritannien aufgebracht. Zu dieser Zeit brachte der Einsatz von stranggepressten Aluminiumkomponenten jedoch keine großen Vorteile, dh die höheren Materialpreise wurden nicht für die Verringerung des Fertigungsaufwands kompensiert. Zu dieser Zeit reduzierte der Einsatz von großformatigen Strukturteilen nur die Produktionsauslastung der Karosserie um 40% und reduzierte das Eigengewicht der 26 m langen Karosserie auf 7,5 t, während das Eigengewicht der 26 m langen Stahlkarosserie 11 t betrug. In den 1970er Jahren widmete die Eisenbahnabteilung der Berechnung der Gesamtkosten der gesamten Lebensdauer von Fahrzeugen (Anschaffungskosten plus Betriebs- und Wartungskosten) mehr Aufmerksamkeit. Sie erkannten, dass der Verbrauch von Zugzugenergie auf dem gleichen Niveau gehalten werden muss, was weitgehend vom Eigengewicht des Rollmaterials abhängt.
Später wurden einige neue technische und technologische Maßnahmen, von denen die wichtigsten Mitte der 1980er Jahre erreicht wurden, wie die Einführung des Extrusionsverfahrens für großformatige Strukturteile der zweischichtigen Schale, die den Bedarf an Querbefestigungen auf ein Minimum reduzierte, die Produktionszeit der Fahrzeugaluminiumkarosserie weiter verkürzt und im Vergleich zu Stahlfahrzeugen um 50% reduziert. und es war möglich, einen zweischichtigen Zylinderkörper nach der konventionellen Methode herzustellen, und dann das Öffnen von Fensterlöchern Schweißvorgänge werden alle im Prozess einheitlicher technischer Operationen durchgeführt, wobei nur teilweise Robotertechnologie und -ausrüstung verwendet werden.
Jetzt, da die Eisenbahnabteilungen allmählich und mehr ihre Beteiligung an der Entwicklung neuer Fahrzeuge reduzieren und Kaufrichtlinien umsetzen, um die anfänglichen Herstellungskosten und zukünftigen Betriebskosten zu senken, haben die Hersteller mehr Freiheit bei der Einführung neuer Strukturen und Materialien, um die technischen Anforderungen der Teilnehmer zu erfüllen und sich an den Entwicklungstrend des Marktes anzupassen. Die extrudierten Aluminiumprofil-Strukturteile haben auch andere Vorteile, indem sie einige strenge Anforderungen an die Fahrzeugstruktur erfüllen. Zum Beispiel kann die Steifigkeit der zweilagigen Schalenextrusionsstruktur sicherstellen, dass der aerodynamische Aufprall, der bei der Begegnung des Hochgeschwindigkeitszuges entsteht, eine besondere Schlagzähigkeit aufweist. Ein weiteres wichtiges Merkmal der Karosserie mit dieser Struktur ist ihre große Längssteifigkeit. Das Verhältnis von Längs- und Quersteifigkeit kann 70:30 erreichen, während das Verhältnis von Stahlkarosserie 40:60 beträgt. Darüber hinaus können Aluminiumprofile auch die Anforderungen an eine gute Außenform erfüllen, ohne den Einsatz von Füllstoffen und viel Handarbeit. Da beispielsweise bei einigen Modellen der Deutschen Bundesbahn kein Füllstoff verwendet wird, kann das Eigengewicht nach der Berechnung zusammen mit der Lackbeschichtung 500 kg betragen.
Die Verwendung von stranggepressten Aluminiumprofil-Strukturteilen stellt Fahrzeughersteller auch vor komplexe Aufgaben. Sie müssen ein Gleichgewicht zwischen Arbeits- und Materialpreisen finden und Designer dazu bringen, sich um dieses Gleichgewicht zu bemühen. Es sollte klargestellt werden, dass Material nur ein Faktor im gesamten Konzept ist. Der Produktionsprozess und der angewandte technische Prozess sollten ebenfalls detailliert formuliert werden, um sie an die Produktionskapazität des Unternehmens anzupassen und ein Gleichgewicht mit der Investition herzustellen.
So hat für die meisten Maschinenbauer die Minimierung der Reserven an Produktionsmitteln oberste Priorität. Die Wahl der Materialien und Verfahren durch die Designer hat einen wesentlichen Einfluss darauf. ABB verfügt über eine Produktionslinie, die jede Woche 8 Fahrzeuge mit Aluminiumkarosserie produzieren kann, wodurch die Gesamtkosten für die Materiallagerung um 8% gesenkt werden. Dieses Gleichgewicht wird jedoch aufgrund der Änderungen im technischen Prozess, die durch die Verwendung von Materialien verursacht werden, leicht zerstört. Zum Beispiel, wenn der Übergang vom Schweißen zum Kleben mehr Tagesreserven erfordert, um den erheblichen Zeitaufwand für das Kleben zu kompensieren.
Ein weiterer führender Anbieter von Aluminiumprofilen für die Schienenfahrzeugherstellung ist das deutsche Unternehmen VAW. Die Führungskräfte des Unternehmens gehen davon aus, dass es einen großen Entwicklungstrend bei der Standardisierung der Fahrzeugstruktur und der Einführung der Moduldesignmethode gibt (dieser Trend wurde aufgrund der Marktnachfrage verstärkt, so dass er von den Herstellern unterstützt wird), und glauben, dass angesichts der Marktnachfrage nach der Regionalisierung des Schienenpersonennahverkehrs in Deutschland Einige private Unternehmen werden mehr darauf achten, eine standardisierte Modulstruktur zu verwenden, um den Anforderungen einzelner Besteller in größerem Umfang gerecht zu werden. Derzeit haben verschiedene europäische Lokomotiv- und Fahrzeughersteller eine Vielzahl von Designideen, die auf dem Moduldesign basieren. Diese Transformation zu Standardisierung und Modularität ist sowohl für Hersteller als auch für Anwender von Vorteil. Die Ausweitung der Verwendung von Aluminiumprofilen im Fahrzeugbau wird den Produktionszyklus aufgrund des breiteren Einsatzes des automatischen Schweißens erheblich reduzieren.
Es ist auch offensichtlich, dass geschweißte Aluminiumkarosseriefahrzeuge eine hohe Schlagbelastung aufweisen, was zur Verbesserung der Fahrsicherheit beiträgt. ABB investierte 1 Million Pfund, um den Zerstörungstest der Aluminiumstruktur zu organisieren und durchzuführen, und erhielt zufriedenstellende und vor allem die erwarteten Testergebnisse. Das Unternehmen hat auch wertvolle praktische Erfahrungen bei der Reparatur der Fehlermethoden von Unfallfahrzeugen gesammelt. Anfang 1994 bewies der von GEC Alstom in Frankreich bestellte Schadenstest am Doppelstock-Pkw-Testmuster des Zuges tgv-2n, dass bei einer Aufprallkraft von 250 t aufgrund der absorbierten Aufprallenergie von 8 mj die Struktur für insgesamt 80 cm extrudiert wurde und die Aluminiumkarosserie als Ganzes intakt blieb.
Gleichzeitig ist das Erkennen der Vorteile der Aluminiumkarosserie nicht ohne Probleme. Die Hersteller von Stahlkarosserielokomotiven und -fahrzeugen äußerten sich besorgt über die Betonung von Aluminium im Herstellungsprozess von Eiszügen in Deutschland und führten 1994 eine Studie durch, um die Überlegenheit von Stahl zu bestätigen. Nach wie vor führt die Verwendung von Stahlkonstruktionen jedoch zu einer Erhöhung des Eigengewichts der Karosserie um etwa 20%.
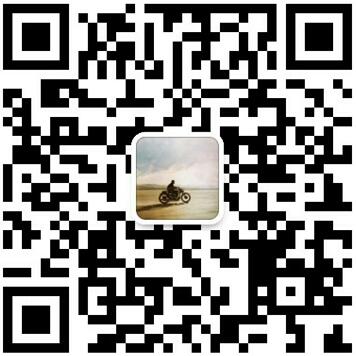
Kostenloses Angebot von Produkten, willkommen jederzeit zu konsultieren, wir werden die erste Antwort geben. Unsere E-Mail: